Issues in the production process in the modern industrial world are common and can harm a company’s efficiency and profitability.
These problems range from minor hiccups to severe failures that can undermine the entire production line.
Reviewing these problems is not only a core part of project managers working in industrial manufacturing but can be a complex and multifaceted challenge.
CONTENT
Identifying and solving these problems involves a thorough grasp of the production process, knowledge of the possible causes of such issues, and the ability to implement effective solutions.
In this article, we will go into detail on dealing with problems in the production process, from techniques for identifying and analyzing causes to choosing and implementing the most appropriate solutions.
1. Identify the problem in the production process
Identifying an issue in the production process is the first and crucial step in reviewing any industrial problem.
This step requires a thorough and detailed analysis of every facet of the production process, and clarity is paramount.
First, it is crucial to ascertain the type of problem. It may be a defect in the final product, such as a poorly assembled part or low-quality material. Alternatively, the problem could be a delay in the production chain, such as faulty equipment or a late material delivery.
Pinpointing the problem is another crucial aspect. Determining exactly where the problem lies in the production process, whether at the beginning, middle, or end of the production chain, is imperative to understanding the entity and impact of the problem.
Identifying the problem often involves using diagnostic tools, visual inspections, or customer feedback. Using advanced technologies, such as sensor technology, can be particularly beneficial at this stage for accurate diagnosis.
Documenting the problem is another crucial step. Documenting the problem clearly and accurately through photos, video recordings, or detailed written reports ensures that all relevant information is available for analysis and resolution.
Communicating the issue to all stakeholders, including team members, suppliers, and, if necessary, customers, is a pivotal step. Clear communication can prevent further misunderstandings or delays and ensure everyone is on the same page.
Assessing the impact of the problem on the production process as a whole is also an important aspect. This assessment can help determine the urgency and priority of the solution, ensuring that resources are allocated appropriately.
Lastly, depending on how intricate the issue is, it may be useful to involve experts in the field, such as engineers or technical specialists. Their experience and expertise can provide a deeper assessment and guidance toward a more effective solution.
2. Analyze what causes the problem
Analyzing the causes becomes the next crucial step after accurately identifying the issue in the production process.
This step involves more than simply identifying the problem and getting to the very core of what caused it. Here is how an effective root cause analysis can be carried out:
- Data collection: Collecting accurate and relevant data is critical. Collecting information from different departments, such as production, quality, and logistics, may be necessary.
- Use of specific tools: Tools such as the Mindzie process mining or the 5 W’s Method (Who, What, When, Where, Why) can be used to analyze root causes.
- Process analysis: Examining existing processes and practices can unveil where errors or inefficiencies may have occurred.
- Staff interviews: Talking to the staff involved can provide valuable insights about the source of the problem.
- Technical assessment: Technical assessment using advanced diagnostic tools, such as 3D scanning or vibration analysis, may be necessary to understand the source of the problem.
- Temporal analysis: Understanding when the problem first occurred can help identify the causes. Trend analysis over time can be beneficial.
- Interdisciplinary collaboration: Working with experts from different fields within the organization can provide a more comprehensive picture of possible causes.
- Environmental impact assessment: External factors such as environmental conditions can sometimes play a factor in the issue. Assessing these aspects can be crucial.
- Documentation and reporting: Creating a detailed report that documents the root cause analysis helps in immediate resolution and future prevention.
Root cause analysis is a complex process that requires a deep understanding of the issue and a systematic methodology to explore all possible causes.
The goal is not only to fix the current problem but also to prevent it from reoccurring in the future. Clarity, precision, and proper tools and techniques are essential to ensure this step is conducted successfully.
3. Implement solutions in the production process
Implementing solutions in the production process is the step where the discoveries made during problem identification and root cause analysis become concrete actions.
Solutions can be simple or complex, but an effective solution usually requires a focused approach.
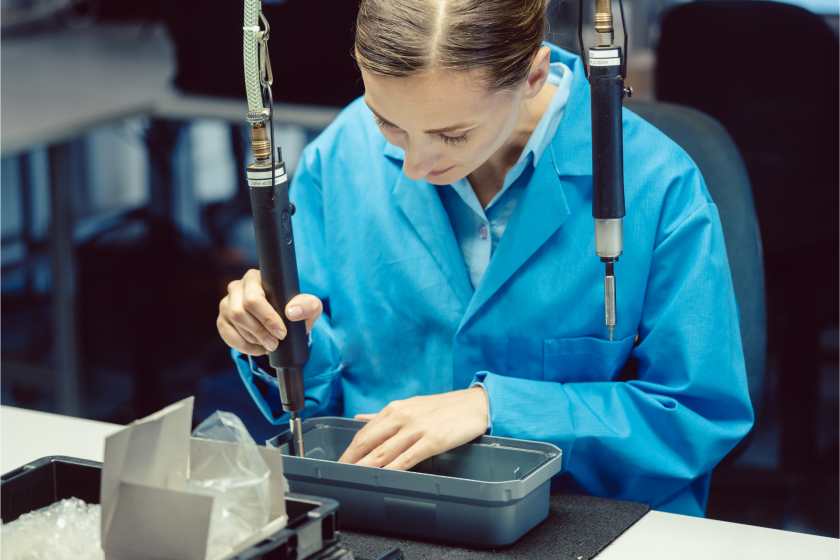
Here are some key aspects to take into consideration:
- Solution definition: First, it is necessary to define the solution clearly. It may be a change in a process, adding a new tool, or providing additional staff training.
- Resource assessment: determining the necessary resources, such as time, money, and manpower, is critical to ensuring that the solution can be successfully implemented.
- Planning: Creating a comprehensive plan with clear deadlines, responsibilities, and goals helps keep implementation on track.
- Interested parties involved: Communicating and involving all interested parties, from employees to suppliers, ensures that everyone is aligned and involved in the process.
- Monitoring and control: Implementation of monitoring and control mechanisms to assess the solution’s effectiveness during implementation may include regular reviews or using software such as Twproject for monitoring.
- Flexibility: Be prepared to adapt to unforeseen changes or obstacles during implementation. Flexibility can be the key to overcoming obstacles.
- Impact assessment: Assess the solution’s impact on the production process as a whole, including long-term effects and possible unintended consequences.
- Documentation: For future reference, document every aspect of implementation, including accomplishments and lessons learned.
- Training and support: Continuous training and support can be essential to ensure the solution is successfully integrated and maintained over time.
- Implementing solutions in the production process is a task that requires considerate planning, clear communication, and effective resource management. Whether the solution is simple or complex, a focused and systematic approach is often the key to ensuring that the solution not only solves the current problem but also helps improve the overall efficiency and quality of the production process.
4. Monitor the production process flow
Constant monitoring is a key step in the process of reviewing a problem in the production process.
It is not just a one-time audit but a regular effort to ensure that the implemented solutions work as intended and that no new problems arise.
Monitoring can be done manually through regular inspections, data reviews, and meetings with staff to discuss the progress of the process. This monitoring requires constant effort and clear communication between all parties involved.
However, in the modern industrial scenario, advanced digital tools can supplement or even replace manual monitoring.
Twproject project management software stands out as a must-have tool in this context. It offers real-time monitoring capabilities that provide instant and accurate insight into the production process.
With Twproject, project managers can set alerts and notifications to be notified immediately if something goes wrong.
They can also use customized dashboards to visualize key metrics and analyze trends over time.
This type of digital monitoring enhances efficiency and accuracy, allowing a quicker response if problems emerge.
Furthermore, constant monitoring through software can facilitate collaboration between different departments and levels of the organization, ensuring that everyone is aligned and informed.
Whether done manually or through tools like Twproject, continuous monitoring requires constant commitment, a deep understanding of the process, and a willingness to adapt and respond quickly to emerging challenges.
5 tips for reviewing a problem in the production process
Reviewing a problem in the production process is a challenging task that requires various skills, tools, and approaches.
Here are some key suggestions that can help guide this process:
- Clear communication: Clear communication is critical at every stage of the process.
Whether identifying the problem, analyzing the causes, or implementing solutions, open and transparent communication can be key to success.
Getting all stakeholders involved and ensuring everyone understands the goals and expectations can prevent misunderstandings and conflicts.
- Constant training: Regular staff training is critical to keep skills up-to-date and aligned with the latest technologies and methodologies. Training can be problem-specific or broader, but it must be ongoing and targeted to be effective.
- Use of project management software: Features like time tracking, team collaboration, and resource allocation can be a powerful ally in reviewing and resolving problems.
- Regular review: Regular review of the production process is not just a response to a problem; it can be a proactive strategy to prevent future issues. Regular performance analysis, inspection of equipment, and evaluation of procedures can detect potential problems before they become serious.
- Flexibility: the industrial manufacturing world constantly evolves, and changes can be swift and unexpected. Being flexible and ready to adapt to new situations can be priceless. Whether it is changes in the market, technologies, or regulations, a flexible mindset can help you successfully navigate these changes.
Problem review in the automotive parts manufacturing industry

Consider a manufacturing industry specializing in producing automotive components, such as brakes, suspension, and steering systems.
The industry is renowned for its high-quality production, but recently it has encountered some issues related to delays in the production chain and defects in some finished products.
Let’s examine how the project manager can deal with these problems:
- Detailed analysis of the issue: First, it is crucial to understand the source of problems. The project manager should work with quality and production teams to pinpoint troublesome areas, including obsolete machinery, unreliable suppliers, or inefficient processes.
- Clear and prompt communication: Maintaining open communication with all stakeholders, including suppliers, customers, and team members, is key. Informing everyone of problems and proposed solutions can prevent misunderstandings and build trust.
- Software implementation: Consider implementing project management software like Twproject to track, analyze, and fix problems. This way, you can improve efficiency and provide a clear view of the production process.
- Regular staff training: Ensuring personnel are properly trained in the latest technologies and methodologies can reduce errors and improve quality. Training should be regular and targeted to the specific needs of the automotive industry.
- Supplier evaluation and improvement: If delays in the delivery of materials are a concern, evaluating and improving supplier relationships may be a solution. This could include negotiating better terms or finding more reliable alternative suppliers.
- Constant monitoring: Implement a constant monitoring system to spot problems before they become critical. This may include regular inspections, quality control, and using sensors and technology for real-time monitoring.
- Flexibility and adaptability: Being prepared to adapt to changes in the market, such as fluctuations in demand or new regulations, is vital. A flexible mindset and a proactive approach can help you navigate these changes successfully.
- Environmental impact assessment: Consider the environmental impact of your production processes and find ways to reduce your carbon footprint. This is good for the environment and can improve your company’s reputation.
By integrating Twproject with other software already in use, the whole process has become fluid and, last but not least, thanks to timely reporting, the company has now a clearer view of project costs.

Reviewing an issue in the production process is a task that demands focus and expertise. Remember, the key may lie in simplicity and clarity. Most effective solutions can be implemented with a focused and systematic approach. When applied carefully and consistently, these suggestions can guide project managers and their teams toward effective and proactive problem management, improving the production process’s overall efficiency and quality.