What cannot be missing in a healthy project management is cost estimation, an essential element for the success of a project, although often unjustly neglected.
CONTENT
A poorly conceived budget leads to misallocation of resources, unrealistic expectations, and, eventually, failure.
Also, the very nature of a project carries risks, which lead to unexpected costs and management issues.
SIt is therefore clear that cost estimation in project management is an arduous task, and yet an interesting challenge to engage in.
So let’s see what it is and some techniques to simplify it.
What is cost estimation in project management?
In project management, cost estimation forecasts the financial resources needed to complete a project within a given scope.
Early estimates are often used in the first planning phase and can determine whether or not a project will move forward.
After a project has been approved, a more detailed cost estimate becomes essential for budgeting to allocate various resources over the lifecycle appropriately.
A complete cost estimate should include both direct and indirect costs.
Getting a budget that minimizes costs while maximizing project quality and scope can be challenging.
And yet it is important to do this exactly, and here we come to you with some techniques to employ.
4 project cost estimation techniques
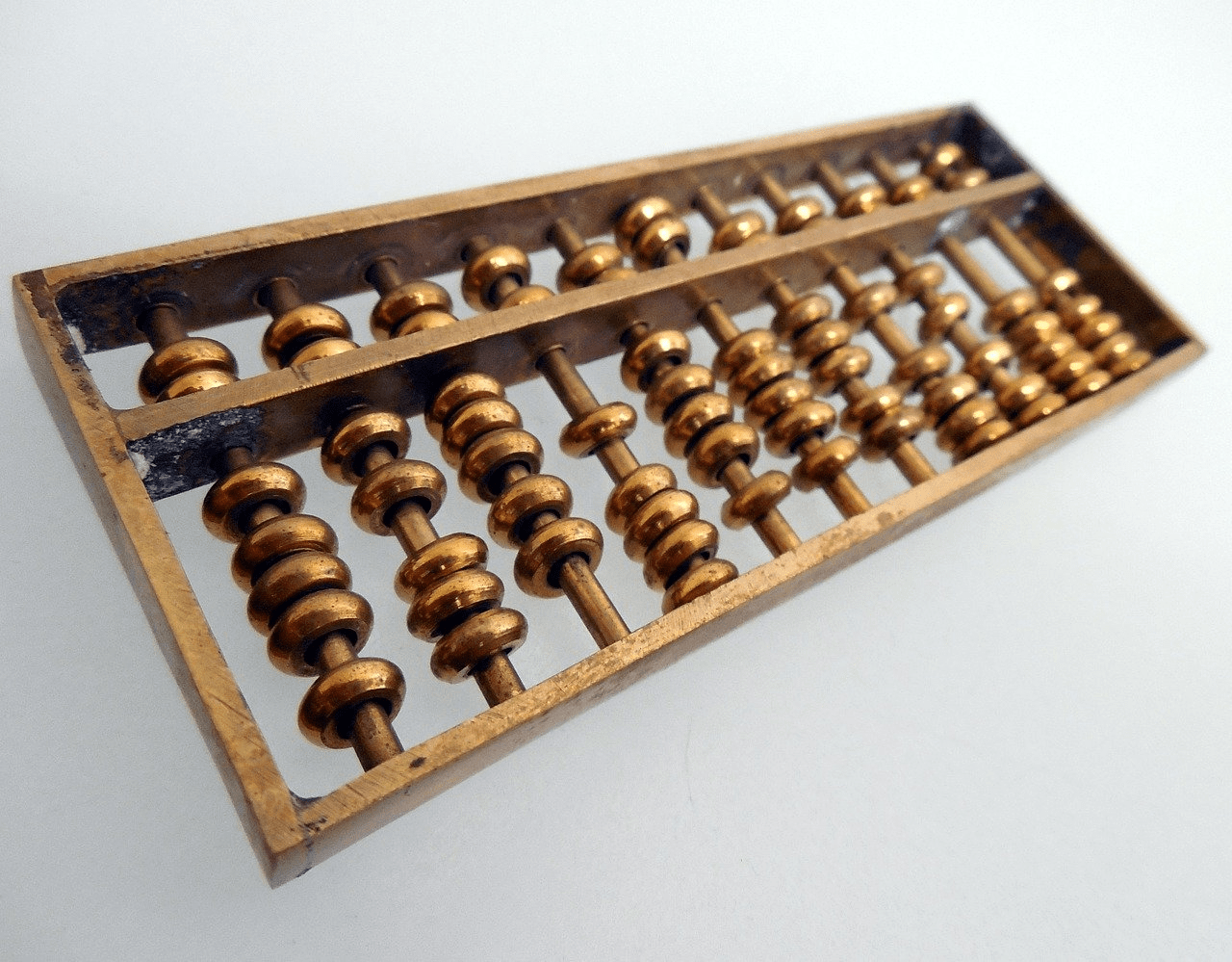
The exact way project managers do a cost estimate depends on different factors.
Some businesses, for example, require that all projects be budgeted based on specific policies, while others may rely on the project manager’s experience.
Here are four of the most common cost estimating techniques in project management:
1. Analogous estimating
Through an analogous estimating technique, a project manager estimates the expected project costs based on the known costs associated with a similar project that has already been completed in the past.
This estimating method involves a mix of historical data and expert opinions from professionals working on the project.
As no two projects are identical, analogous estimating has some limitations.
This technique is often used in the early stages of project planning, when a rough estimate may be enough.
Alternatively, analogous estimating can be used when there is not enough detailed information about the current project.
2. Parametric estimating
The parametric estimating technique uses historical data and statistical modeling to attribute a monetary value to specific project resources.
It is a significantly more accurate method than the analogous estimation seen above, but it requires more early data to estimate costs accurately.
This technique is often used in the construction and building industry.
One example might be: an experienced construction manager may know that, on average, the square meter of a new building costs a given amount.
Having this average cost known, as well as the error margin and square footage of the new project, parametric estimating will help identify a relatively certain budget.
Please note, however, that in this case, the data source must be accurate; otherwise, the entire estimation would be incorrect.
3. Bottom-up estimating
In bottom-up estimating, a larger project is split into several smaller pieces of work.
Then, the project manager estimates costs for each of these smaller work packages individually.
For example, if a project involves work that will be divided among multiple departments within an organization, then costs might be split by department.
Once all costs have been estimated, they are counted and summed into a single larger cost estimate for the project as a whole.
Since bottom-up estimating allows a project manager to examine each activity within a project in more detail, this technique generally provides for a very accurate estimating process.
4. Three-points estimating
In the three-points estimating, based on the experiences of similar past projects, three separate estimates are defined for those costs associated with a project:
- An “optimistic” estimate (a), where work is ideally carried out by spending funds as efficiently as possible;
- A “pessimistic” estimate (b), which is the worst scenario, where funds are spent, and work is done in the absolute least efficient way;
- The “most likely” scenario (m), which generally lies somewhere in the middle and is the most realistic estimate.
From these three numbers, through exact formulas, the weighted average and standard deviation are calculated:
E = (a + 4m + b) / 6
DS = (b – a) / 6
Standard deviation is used to estimate probability.
This technique, when employed correctly, provides a very accurate estimate and, thus, successful cost planning.
It is therefore evident, after these considerations, how cost estimation is a key element in project management.
With Twproject we can manage and have control over all our projects including their budgeted costs vs. realized final costs

Not only is budgeting considered when deciding whether or not a project should be undertaken, but it must also be regularly monitored so that work can be successful.
When estimating and monitoring project costs, it is crucial to use good tools to calculate a more accurate project budget.
Twproject allows you to keep track of a project’s costs through its multiple features, providing essential support to a project manager’s work.
Hi,
I think you made best guide on cost estimating in project management. I can’t tell you how helpful information you made for us. Thanks for the sharing knowledge on this topic.
Hi,
Thanks for making the content on Project Management along with cost estiamting techniques. Your content helped me a lot teaching things i didn’t have before. Please keep sharing knowledge like this. Once again thanks..