Corrective and preventive actions are processes used to identify, record, and address defects, deficiencies, and nonconformities.
CONTENT
These are also called “CAPA” (“Corrective Actions Preventive Actions”) and constitute an organization’s immune system.
Typically, corrective action, preventive action, and defect repair are terms commonly used in project quality management.
Defect correction is a simple concept, yet distinguishing corrective action and preventive action can be difficult; in fact, the difference between actions is so minimal that many people get confused.
What is the CAPA? Why is it essential to the quality of the project?
CAPA, as stated previously, is the abbreviation for Corrective Actions Preventive Actions.
These two aspects of CAPA are usually connected, but here’s the main difference between the two:
- Corrective action: elimination of the cause(s) of an existing non-conformity or undesirable situation in order to prevent its future recurrence.
- Preventive action: identification and elimination of the causes of potential nonconformities in order to prevent their occurrence.
In standards-based quality certifications such as ISO 9000 for example, the preventive action description directly follows the corrective action description, which has led to the misconception that the two processes should work together.
Actually, they are two separate paths and preventive action ideally precedes corrective action to prevent or avoid the need for corrective action.
Thus, corrective action is reactive, while preventive action is proactive. But why is it essential to project quality?
Because integrating CAPA into quality management systems allows you to anticipate risks, reduce costs associated with repeated errors and continuously improve processes, products and results.
In a well-managed project, preventive actions help keep the project on track in terms of time, budget and quality, by taking action after identifying warning signs or weaknesses in the processes.
Corrective actions, on the other hand, allow you to respond to existing problems in a structured and documented manner, preventing the same errors from recurring.
Together, these actions ensure continuous improvement and project reliability, two key elements for achieving customer satisfaction and compliance with quality standards.
Implementing CAPA effectively means moving from reactive management to conscious and strategic management, where every deviation from the plan is an opportunity to learn, improve and consolidate the overall quality of the project.
What does corrective action mean?
Corrective action means identifying, documenting and eliminating the root cause of a nonconformity or problem to prevent the problem from repeating.
Corrective actions are looked at in more detail than corrections – which solve immediate problems – and corrective actions are typically implemented over a slightly longer period of time to prevent recurrence.
For example, if you put a bucket under a leaky pipe, this is a correction because it solves a problem immediately. However, if you inspect the entire sink and drain and notice that the pipe is dripping and clogging repeatedly due to a damaged gasket which is then replaced, this is a corrective action.
Corrective Process Steps
Here are some steps you can find in a corrective process:
- Identifying and documenting the problem promptly. Ask questions to obtain details and determine if this is a one-time event or if it has the potential to recur.
- Implementing a temporary fix, mitigation, or repair.
- Determining the cause of the problem.
- Determining the solution that will prevent the problem from recurring. Solutions may include new parts or process changes.
- Implementing corrective action and making sure everything is reported.
- Verifying that the action continues to be effective and that the problem does not recur.
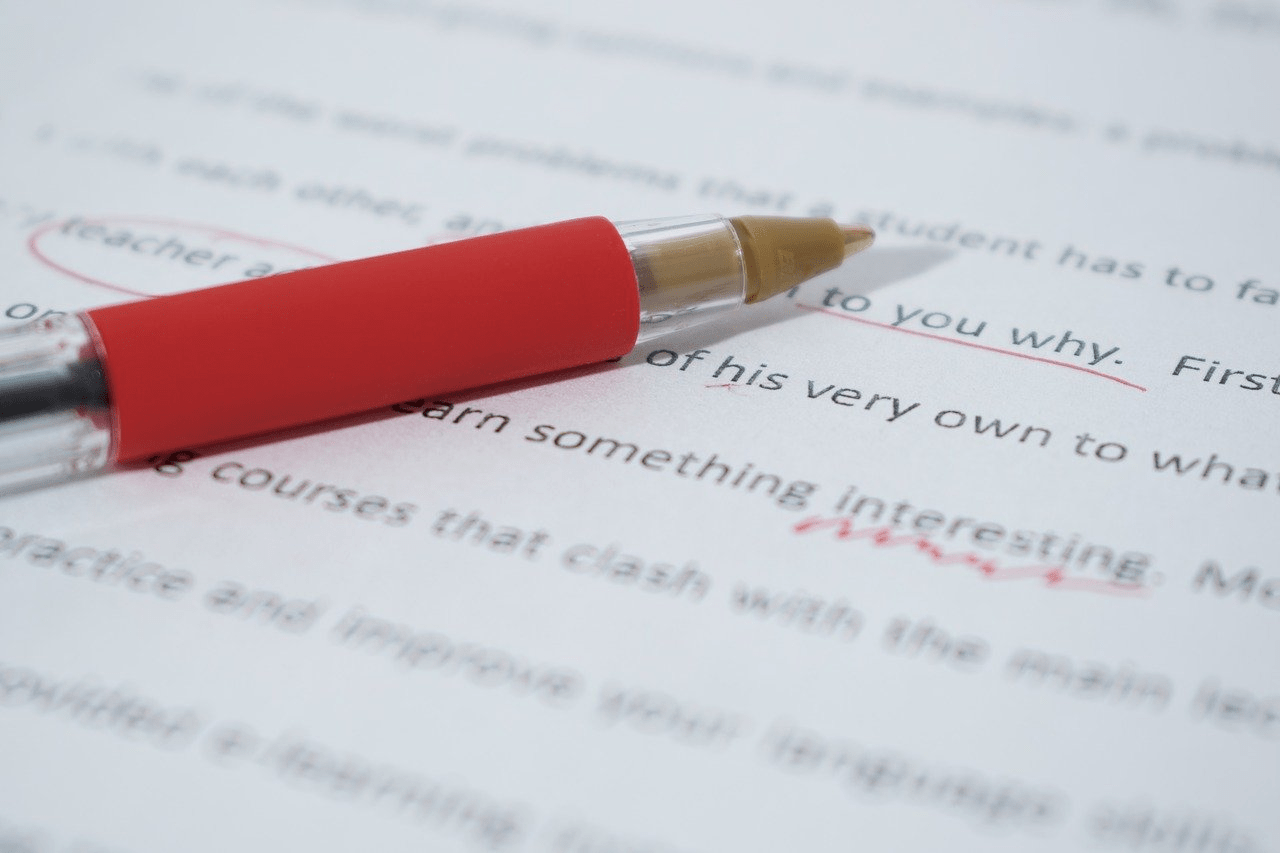
What is preventive action?
Preventive action is now considered a part of good planning and proper risk analysis and management.
This fully embraces the idea that prevention comes first and eradicates problems and, therefore, the necessity for corrective action.
Preventive action determines what in a project might deviate from the chosen path and cause, for example, over budget or low quality output.
A good example, referring back to the previous one, would be to check the pipes and drains of all the sinks present to see if certain parts should be replaced before they fail.
A preventive action process, besides including a specific preventive action plan to mitigate potential problems, also includes implementing controls to ensure that any preventive measures continue to work.
Preventive action means identifying not only potential problems, but also improvement potential opportunities.
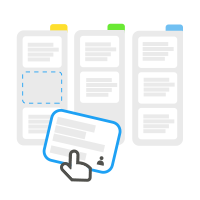
Try Twproject and manage corrective/preventive actions with a single click.
Click here for a free trial!Popular – yet wrong – ideas about CAPA
Although regulations may require organizations to properly record CAPA processes and adhere to them, organizations often have the following misconceptions about this concept:
- It is a punishment because something went wrong
- It’s extra work. The solution is to set up a review board with people trained in appropriate roles so that CAPA becomes a regular responsibility.
- Training is too expensive. Management often complains that neither budgets nor programs offer resources for training employees in the efficient implementation of CAPA, yet you can save money by setting up a process.
CAPA is easier with a little help
Companies will always find flaws in their products or processes, but there will always be room for improvement, and that is the reason why, using a project management software is crucial.
Corrective action is an activity that has been determined to correct or resolve a present problem, while preventive action is defined as an activity identified to prevent a problem that may occur in the near or distant future, both, with a software like Twproject can be determined easily.
Twproject will show any delayed projects in real time and issues incurred for corrective actions and, at the same time, can create a knowledge base for preventive actions for future projects.
Although the purpose is different for both, preventive and corrective actions are created to address issues in the past, present, or future.
The ability to identify risks and help identify corrective and preventive actions is an important skill that organizations can – and should – develop and use to their advantage at the expense of the common, but misconceptions surrounding CAPA.